A ragasztás alapfogalmai
A faipar, és vele együtt a bútoripar, egyik leglényegesebb munkafolyamata a ragasztás. A fa a nedvesség hatására dagad, zsugorodik, és vetemedik is. A fában keletkező feszültségeket azonban nagymértékben csökkenthetjük azáltal, hogy a fatestet kisebb részekre vágjuk, s a feldarabolt részeket azután ragasztással ismét egyesítjük. De a minőségjavító hatáson kívül a ragasztásnak gazdasági előnyei is vannak, hiszen a kisebb részek összeragasztásával a leszabásnál csökkenthetjük a keletkező hulladék mennyiségét. És a furnérozás, (a nemesebb fafajták takarékos felhasználása érdekében) valamint a bútorkészítésnél használt különböző szerkezeti kötések kialakítása sem képzelhető el ragasztás nélkül. A ragasztást, mint forgácsolásmentes faipari alakító eljárást számos területen használjuk. fakötések rögzítése, táblásítás tömbösítés, hossztoldás, furnérozás, lemezelés, forgácslap gyártás…
A ragasztás alkalmával a ragasztandó felületek közé egy harmadik anyagot viszünk, mely képes arra, hogy a felületeket egymással tartósan egyesítse. Ez az anyag a ragasztóanyag. Ragasztás után az összeragasztott felületeket csak erőkifejtéssel lehet szétválasztani.
A ragasztóanyag megválasztásakor figyelembe kell venni:
- A ragasztandó termék rendeltetésszerű használata során várható nedvességtartalmi változásokat
( Más-más vízállósági fokozatú ragasztóanyagot kell ugyanis használnunk, ha a késztermék egy száraz szobába, egy fürdőszobába, vagy a szabadba, egy az időjárás viszontagságoknak kitett területen kerül felhasználásra.)
- Az alkalmazása során fellépő nyugalmi (statikus) vagy változó (dinamikus) igénybevételeket( rugalmasabb ragasztóanyagot használjak, vagy elegendő e az olcsóbb, ridegebb is…)
(A statikus igénybevételnél az elkészített termék állandó nagyságú terhelésnek van kitéve. Hasonló terhelést jelent a szék számára egy rajta ülő ember. Ha azonban az illető elkezd billegni a székkel, azt dinamikus igénybevételnek teszi ki. A székre ható erők ebben az esetben folyamatosan változnak egy minimum-, és egy maximum érték között. A dinamikus terhelés lényegesen nagyobb igénybevételnek teszi ki a terméket, így a ragasztóréteg fokozottabb rugalmasságát követeli meg.)
– A fenti tulajdonságokon túl figyelembe kell vennünk azt is, hogy a rendelkezésünkre álló technikai berendezések milyen típusú ragasztóanyag használatát teszik lehetővé.
A legmegfelelőbb ragasztóanyagot fenti szempontok széleskörű figyelembevételével tudjuk megválasztani.
A gyártmány rendeltetésszerű használata során várható nedvességtartalmi és hőmérsékleti hatásokat a ragasztók vízállósági kategóriáinak ismeretével vehetjük figyelembe. Hogy a gyártmány rendeltetésszerű használata során várható nedvességtartalmi és hőmérsékleti hatásokat a legegyszerűbben eldönthessük, a ragasztóanyagokat vízálló fokozatokba soroljuk:
(E vizsgálatához próbatesteket készítenek. Az összeragasztott próbatesteket 24 órán át vízben áztatják(D1-D3), vagy kétórás főzésnek teszik ki (D4). A ragasztóanyag vízzel, ill. főzéssel szemben nem ellenálló, ha a ragasztás szilárdsága az eljárás során csökken, vagy megszűnik.)
- Nem vízálló a Dl : felhasználható zárt belső terekben, ahol nem kell számolnunk páralecsapódással, és a hőmérséklet legfeljebb rövid időre haladja meg az 50 °C-ot, a fa nedvességtartalma pedig nem lépi túl a 15%-ot. Leginkább szobabútorok, és belső ajtók ragasztásához használják, és ne felejtsük el, hogy a tömbösített belsőajtó frízek elkészítésénél is ezt használják, így abból nem készíthetünk, ennél fokozottabb hő és nedvességhatásnak kitett termékeket.
- Mérsékelten vízálló a D2: Ugyancsak belső terekben használható, de ez a ragasztóanyag már ellen tud állni a magasabb légnedvességnek és az alkalmanként, rövid ideig tartó lefolyó vagy lecsapódó pára, hatásának.
- Vízálló a D3 : Külső, de időjárástól védett területeken használhatjuk, illetve zárt térben, ha a magasabb légnedvesség és a rövid ideig tartó lefolyó vagy lecsapódó pára hatásával gyakrabban kell számolni.
- Főzésálló a D4 : felhasználható belső terekben, amennyiben gyakori erős lefolyó vagy lecsapódó víz hatása jelentkezik, és időjárási hatásoknak kitett külső területén, megfelelő felületi védelemmel.
A D4-es ragasztó nem „erősebb” normál körülmények között, mint a D2. A különbség csak vizes hatásokra (párás klíma, fröccsenő víz stb.) érzékelhető.
Ezen ragasztóanyagok árai között jelentős különbségek jelentkeznek. Ezért, a gazdaságosság érdekeit szem előtt tartva, érdemes mindig azt a vízállósági fokozatú ragasztóanyagot alkalmazni, mely minimálisan ki tudja elégíteni, az elkészítendő gyártmánnyal szemben támasztott ragasztási követelményeket.
A bútor- és belsőépítészet leggyakrabban alkalmazott fa alapanyagai a faforgács lap, az MDF- és HDF-lapok, valamint a rétegelt lemezek. Minden lemezféleségnek meghatározott vízfelvételi tulajdonságai vannak: ez egy nagyon fontos paraméter, ha például diszperziós ragasztókkal dolgozunk. Emellett ha nedvességre aktiválódó ragasztót alkalmazunk, az alapanyag saját nedvességtartalma ugyancsak fontos jellemző. Egyre gyakrabban kerül sor a fentiektől eltérő lapféleségek furnérozására. Itt szóba kerülhetnek az ásványi anyag kötésű tűzálló lemezek, a fém, mint pl. az alumíniumlemezek, a műanyag lapféleségek, az üveg mint hordozóanyagok. Minden lapféleségre áll, hogy azokat mechanikailag jól meglehessen munkálni. Párhuzamos, sík felületűek legyenek, hogy préselésnél ne keletkezzenek hibák. A legkisebb hibák is gyorsan összeadódhatnak, ezért fontos a faanyagoknál a kalibráló csiszolás és portalanítás. A furnérok kiválasztásánál és előkészítésénél az alakisági szempontok minden bizonnyal a legfontosabbak. A ragasztás eredményességét a fafaj mellett a furnér előkészítése is lényegesen befolyásolja. A furnérok illesztését nagyon pontosan kell elvégezni ahhoz, hogy a nyitott fugát elkerüljük. A hullámos furnérok különös gondosságot, gyakorlatot igényelnek ahhoz, hogy ne keletkezzenek repedések.
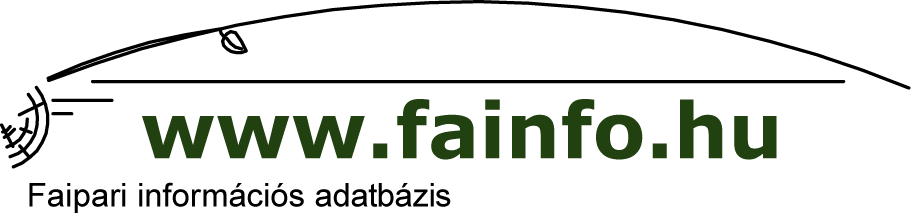


Ezt a korlátot egy vállalkozó, D2 ragasztóanyag használatával készítette, kültérre. Ezt az állapotot azonban nem csak ez a hiba eredményezte. A korlát alapanyaga nedves, gőzöletlen bükk faanyag volt. A bükkfa a legjobban vetemedő fafajunk, épp ezért a Thonett székek megjelenéséig, az 1800-as évek közepéig, csak tüzifaként használták. A gőzölés megjelenése tette széleskörűen alkalmazhatóvá. Ezt sokan hajlamosak elfelejteni.
A ragasztás során fellépő erők
A ragasztás során a felületek közötti kötés akkor jön létre, mikor a ragasztóanyag folyékony halmazállapotúból szilárd halmazállapotúvá változik (mikor a ragasztóanyag kikeményedik). A kikeményedést követően a ragasztóanyag egy olyan szilárd kötést biztosít a felületek között, mely ellenáll a mechanikai erőhatásoknak. A ragasztó által kialakított kötésnek több összetevője van: nagyságát, kémiai (adhéziós és kohéziós), illetve mechanikai erők összességével írhatjuk le.
Mechanikai erő: A faanyag, az őt felépítő sejtek kapillár porózus rendszere. A felületre felhordott folyékony ragasztóanyag beszívódik a faanyag rostjai közé, ahol a kikeményedést követően, saját anyagából változatos alakú, mikroszkopikus csapocskákat hoz létre. Az egymáshoz ragasztott anyagok felületén található üregekbe folyt ragasztóanyag, ezen csapocskák segítségével mechanikai kötést hoz létre.
A kohéziós erő: A szilárd anyagot felépítő atomok és molekulák között ébredő összetartó erő. Jelen esetben a ragasztó molekulái között létrejövő összetartó erőt értjük alatta. Vonzó- és taszító komponensekből tevődik össze, de a vonzóerő általában jóval fol
Adhéziós erőnek hívjuk a különböző típusú anyagok, esetünkben a faanyag és a ragasztóanyag között fellépő, tapadást okozó összetartó erőt.
Ha a faanyag vonzóereje kisebb, mint a folyadék molekuláit összetartó belső kohéziós erő, a ragasztóanyag nem terül el a faanyag felületén, hanem különböző cseppek formájában összeáll a felületen, ragasztóanyaggal be nem vont területeket képezve. alakjában megmarad a felületen. Ez főleg akkor fordul elő, ha a felület szennyezett (pl. poros), vagy a faanyag túlságosan olajos, zsíros, vagy gyantás. A ragasztó csak tiszta felületen terül jól. Ezért a ragasztás megkezdése előtt komoly figyelmet kell szentelni a felületek tisztítására. A fafaj, a szöveti szerkezet, és a kémiai tulajdonságok nagy mértékben befolyásolják a ragasztó adhézióját.
Ragasztással kapcsolatos alapfogalmak:
Kötési szilárdság:
az összeragasztott felületek között ébredő összetartó erő. Mértékegysége N/cm2. Mely a ragasztott felületek 1 cm2-ének szétválasztásához szükséges erőt jelenti.
Megfelelő ragasztás esetén, a létrehozott kötés erősebb, mint a faanyag rostjait összetartó erő, így a felületek a ragasztás síkja mellett válnak el egymástól. A felület szálkásan kiszakadozott lesz.
Rugalmasság:
A faanyagok ragasztásával kapcsolatos alapvető követelmények között szerepel, hogy a ragasztóanyag segítségével létrehozott kötés megfelelően rugalmas legyen. A megszilárdult ragasztórétegnek le kell tudnia követni a faanyag alakváltozásait, anélkül, hogy a ragasztás berepedezne. ( A szerkezetek igénybevételekor fellépő deformációk közben létrejövő repedések ugyanis az idők során, csökkentik a ragasztás szilárdságát.
A ridegség különösen a műgyanta ragasztókra jellemző. Karbamid-formaldehid ragasztóanyagoknál különböző töltőanyagok, PVAc ragasztóknál lágyítók hozzáadásával javíthatjuk a kialakított kötés rugalmasságát.
Fazékidő:
Az az időtartam, ameddig a bekevert, ragasztáshoz előkészített ragasztóanyag felhasználható marad. Egykomponensű ragasztóknál megegyezik a csomagoláson feltüntetett szavatossági idővel. Kétkomponensű, vagy előkészítést igénylő ragasztóanyagoknál, az értéket a ragasztó műszaki adatlapja tartalmazza.
Érlelési idő:
Főleg a por alakú ragasztóanyagokra jellemző. A bekeverésétől a használatra való alkalmasságig eltelő idő. Kazeinenyveknél, a teljes oldódás után az elkészített enyvet felhasználás előtt kb. 15-20 percig kell állni hagyni.
Nyílt idő:
az az időtartam, amely a ragasztóanyag felületre történő felhordása és a préselés között eltelhet, anélkül, hogy a ragasztóréteg megszilárdulna. A túlságosan nagy nyíltidő a ragasztási szilárdság nagymértékű csökkenését okozhatja, de alacsony viszkozitású ragasztóknál a rövid nyíltidő is csökkenti a szilárdságot, mivel a ragasztóanyag nem képes egyenletesen elterülni a felületen. Ez az az időszak, mely alatt (a ragasztó felhordását követően) az alkatrészeket feltétlenül össze kell illeszteni!
Zárt idő: A ragasztandó alkatrészek összeillesztésétől a préselés megkezdéséig tartó idő.
A zártidő általában jóval hosszabb a nyíltidőnél, hiszen a ragasztandó felületeket a ragasztó felhordása után többnyire azonnal egymásra helyezik. Hatása a ragasztási szilárdságra jóval kisebb, mint a nyíltidőé. A hosszabb nyílt-, és zárt idő segíti a munkaszervezést, de a legnagyobb szilárdság, minimális nyílt- és zártidők alkalmazása esetén érhető el. Ha ezeket a feltételeket nem tudjuk biztosítani, kétoldali ragasztóanyag- felhordással tudunk javítani a kialakítandó kötés szilárdságán.
présidő:
a ragasztóanyag kikeményedési idejéig eltelő idő, ameddig a ragasztott felületeket összeszorítva kell tartanunk.
Kikeményedési idő: az, az időtartam, mely alatt a ragasztás öntartóvá válik.
A kikeményedési idő eltelte után a présnyomás megszüntethető, a ragasztott szerkezet szállíthatóvá válik, de még nem tehetjük ki nagyobb terhelésnek.
Kötési idő: az, az időtartam, amely alatt a ragasztó eléri a teljes kötőszilárdságot. A ragasztás a kötési idő letelte után válik terhelhetővé.
Szárazanyag-tartalom: A ragasztóanyagban található szilárd részek és a teljes ragasztómennyiség súlyának aránya. Megmutatja, hogy a teljes megkötés után visszamaradó szilárd ragasztóréteg, hány százaléka a felvitt anyagmennyiségnek. Minél nagyobb a ragasztó szárazanyag-tartalma, annál kisebb a ragasztóanyag zsugorodása a kikeményedés során, és az annál jobban kitölti a felületi egyenetlenségeket. Ezt az értéket pl. vizes diszperziós ragasztó esetében 3 órán át 105 °C-on szárítva kapjuk meg.
töltőanyag: Szaporító-, vagy sűrítőanyagnak, is nevezzük őket. A ragasztókhoz keverve növelik a szárazanyag-tartalmat és a viszkozitást (mely segíti a fugák kitöltését, és furnérozáskor csökkenti az enyvátütések veszélyét). Erre a célra legtöbbször különféle ásványi őrleményeket krétaport, kaolint, vagy falisztet használunk. Mennyiségük növelésével a ragasztási szilárdság rohamosan csökken, és az ásványi őrlemények jobban igénybe veszik a szerszámok élét.
Kaolin: a porcelángyártás alapanyagaként használatos alumínium-szilikát-fajta. Fehér, sárgás, illetve barnás vagy zöldes árnyalatú por. E 559-es kóddal, az élelmiszer ipar csomósodásgátló anyagként is használja.
A nyújtóanyagok azonban önmagukban is képesek ragasztott kötések kialakítására. Állati vagy növényi eredetűek lehetnek. (pl.: glutinenyv véralbuminenyv, rozsliszt, keményítő…)
Ezek csökkentik a kikeményedett ragasztóréteg ridegségét, s habár a kötés vízállóságát hátrányosan befolyásolják, nagyobb mennyiségben (20-40%) sem rontják jelentősen a ragasztási szilárdságot.
Mind a töltő-, mind a nyújtóanyagok jóval olcsóbbak a ragasztónál, így gazdaságosabbá teszik a ragasztó-felhasználást.
a viszkozitás a ragasztóanyag sűrűségét, folyékonyságát jelenti. Meghatározza a ragasztófelhordás módját, és szorosan összefügg a ragasztás egyéb paramétereivel (pl. nyílt-, zárt idő). Az alacsony viszkozitású ragasztók szinte bármivel felhordhatók, de a magas viszkozitású anyagok csak speciális felhordóhengerekkel vihetők fel a felületre. Legismertebb a Ford-pohárral mért viszkozitás-mérési mód.
A Ford pohár egy 100 ml térfogatú, 5 mm-es kiöntőnyílású alumíniumedény. A viszkozitást a ragasztóanyag átfolyásának ideje határozza meg. A hígabb ragasztó rövidebb, a sűrűbb ragasztó hosszabb idő alatt folyik ki a pohárból.
Minél viszkózusabb a ragasztóanyag, annál kisebb a nedvesítő-képessége, és annál nehezebben szívódik be a fába, így a ragasztási felület csökkenésével csökken a ragasztás szilárdsága is. Állandó koncentrációjú enyveket vizsgálva azt tapasztalhatjuk, hogy a viszkozitás növekedésével a ragasztási szilárdság is nő.
Katalizátor ( edző): A kémiai úton kötő ragasztóknál a ragasztó kikeményedése egy kémiai folyamat eredménye. A reakció beindításához, a ragasztót egy másik vegyi anyaggal, a katalizátort kell összekeverni. (Néha a katalizátort az egyik anyagra, a ragasztót a másikra visszük fel, és a felületek összeillesztését követően, már a présben indul be a kémiai reakció.)
Kapillár: A faanyag sejtjei hosszú rendkívül kis átmérőjű csövecskéket hoznak létre. A nedvesítő anyagokat, mint pl. a ragasztóanyagokat, az ezen csövekben létrejövő un. kapilláris erő az edények-áledények belsejébe juttatja, ahol a kikeményedést követően alakzáró kötés jön létre.

A viszkozitás a ragasztóanyag sűrűségét, folyékonyságát jelenti. Meghatározza a ragasztófelhordás módját, és szorosan összefügg a ragasztás egyéb paramétereivel (pl. nyílt-, zárt idő). Az alacsony viszkozitású ragasztók szinte bármivel felhordhatók, de a magas viszkozitású anyagok csak speciális felhordóhengerekkel vihetők fel a felületre. Legismertebb a Ford-pohárral mért viszkozitás-mérési mód. Minél viszkózusabb a ragasztóanyag, annál kisebb a nedvesítő-képessége, és annál nehezebben szívódik be a fába, így a ragasztási felület csökkenésével csökken a ragasztás szilárdsága is. Állandó koncentrációjú enyveket vizsgálva azt tapasztalhatjuk, hogy a viszkozitás növekedésével a ragasztási szilárdság is nő.
Katalizátor ( edző): A kémiai úton kötő ragasztóknál a ragasztó kikeményedése egy kémiai folyamat eredménye. A reakció beindításához, a ragasztót egy másik vegyi anyaggal, a katalizátort kell összekeverni. (Néha a katalizátort az egyik anyagra, a ragasztót a másikra visszük fel, és a felületek összeillesztését követően, már a présben indul be a kémiai reakció.)
A Ford pohár egy 100 ml térfogatú, 5 mm-es kiöntőnyílású alumíniumedény. A viszkozitást a ragasztóanyag átfolyásának ideje határozza meg. A hígabb ragasztó rövidebb, a sűrűbb ragasztó hosszabb idő alatt folyik ki a pohárból.

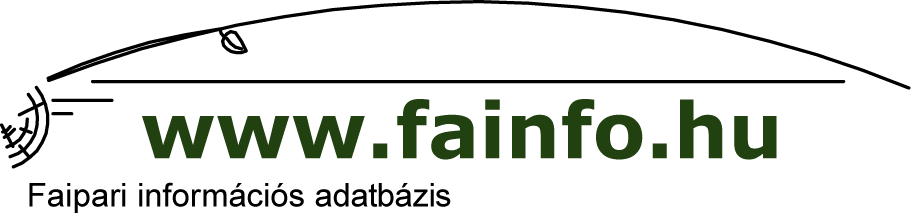